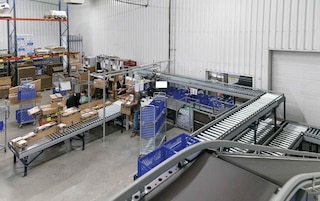
Rotura de stock: ¿qué es y cómo evitar que se produzca?
Se produce una rotura de stock cuando al recibir un pedido de cierto producto o materia prima por parte del cliente, la empresa no dispone del mismo en los almacenes en las cantidades y condiciones demandadas.
Por ello, la compra no puede verse satisfecha y esta incidencia genera unas consecuencias muy negativas, ya que no solo se pierde la venta, sino que la imagen de la propia empresa queda dañada ante el cliente.
En nuestro artículo repasamos los conceptos clave relacionados con las roturas de stock: cómo se calcula el indicador, qué causas y consecuencias tiene este fenómeno y cuáles son las principales estrategias que seguir para evitar que se produzcan.
1. Índice de rotura de stock
Toda maniobra de gestión de stock se sostiene sobre un delicado equilibrio entre la demanda del producto y su existencia en el almacén. La rotura de stock llega cuando este equilibrio se quiebra.
Dentro de los KPI que medir como parte de la gestión logística se encuentra el índice de rotura de stock, que se calcula de la siguiente forma:
Índice de rotura = pedidos no satisfechos / pedidos totales x 100
2. Consecuencias de las roturas de stock
La consecuencia directa de una rotura de stock es un aumento de los costes logísticos. El riesgo de rotura de stock es mayor en el contexto actual porque las empresas se enfrentan al desafío de que a más inventario, mayores son los costes ligados al almacenamiento logístico, por lo que en general las compañías están tendiendo a limitarlos al máximo. En torno a esta idea han nacido metodologías como el just-in-time o el cross-docking.
En este sentido, resulta complejo calcular todas las pérdidas que se derivan de ello. Así, el importe resultante siempre será aproximado, pues en la rotura de stock entran en juego factores subjetivos.
Por un lado, se encuentra la pérdida clara de la venta concreta que no puede satisfacerse (valor objetivo). Pero también hay que contemplar otros aspectos, como que se haya originado una fuga de clientes hacia empresas de la competencia en busca del producto demandado (valor subjetivo).
Además, hay un daño en la imagen de la marca que, en ámbitos como el de la logística de e-commerce, supone una pérdida de confianza y es un grave freno para la demanda futura (valor subjetivo).
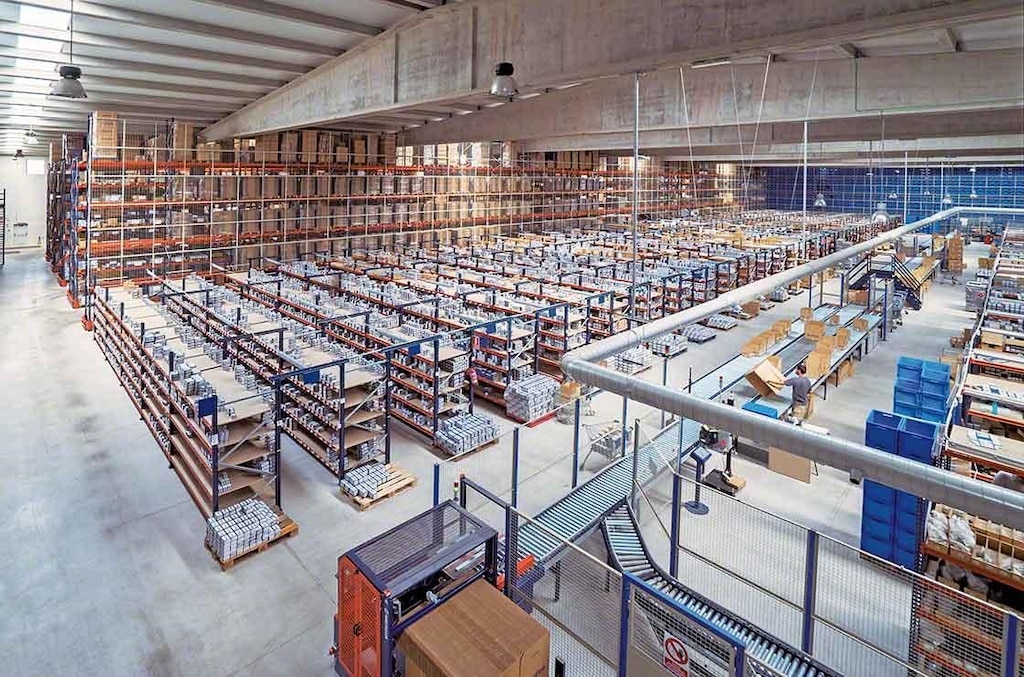
3. Causas de las roturas de stock
Las causas de las roturas de stock son de diversa índole y pueden localizarse en distintos puntos en la cadena de suministro. Como ejemplos, podemos citar las siguientes:
- Un aumento inesperado de la demanda: un ejemplo muy habitual es el del “juguete favorito” que se pone de moda cada Navidad. Al ser el lead time de producción y distribución mayor al margen que dan las fechas, suele producirse una rotura de stock de manual.
- La planificación deficiente de la demanda: las tareas de demand forecasting se encuadran en uno de los ámbitos más desafiantes de la logística. Para estimar la demanda futura, hay que analizar una gran variedad de datos, entre los que se encuentran el histórico de ventas o la estacionalidad y fechas clave.
- Falta de exactitud entre los datos de inventario registrados y la realidad, por fallos humanos a la hora de ubicar los productos o al actualizar los datos de stock.
- Retrasos en el transporte: si la recepción de mercancías en el almacén se produce más tarde de lo planificado, esto puede provocar un retraso en las fechas de entrega para el cliente final.
- Retrasos de los proveedores: si son productores, la falta de un solo tipo de materia prima puede ralentizar toda una línea de producción.
- Fallos humanos en distintos puntos de la cadena de suministro.
4. Estrategias de gestión eficiente para evitar roturas de stock
- Llevar a cabo una adecuada previsión de la demanda
En un entorno altamente variable como al que se enfrenta la logística hoy en día, hay que tratar de limitar la incertidumbre en los pronósticos de demanda y ajustar el aprovisionamiento al máximo. De hecho, en esta área se da una de las aplicaciones del Big Data con más potencial en logística.
Para lograr un pronóstico de la demanda sólido y, en cierta medida, prevenir roturas de stock, hay que:
- Tener claro que en toda predicción hay que contemplar un margen de error estimado.
- Identificar el ciclo de vida en que se encuentran los productos: lo más natural es que pasen por las etapas de introducción en el mercado (novedad), crecimiento, madurez y declive.
- Prever los picos de actividad en días clave y tener en cuenta la estacionalidad del sector.
- Calcular las previsiones para periodos de tiempo lo más cercanos posibles, ya que el futuro lejano es más incierto que el próximo. Conseguir operar con un lead time reducido ayuda mucho en este sentido.
- Contar con un sistema informático que vertebre los procesos en la cadena de suministro
La implantación de un software especializado en la gestión empresarial se ha revelado como una potente estrategia de control y optimización de los flujos logísticos. Debido a la alta complejidad de los procesos, normalmente se requiere una integración de diferentes tipos de sistemas.
En esta línea, destaca el ERP (Enterprise Resource Planning) como elemento vertebrador unido a sistemas más específicos como el software de gestión de almacenes o los programas de gestión de flotas de transporte.
Uno de los principales objetivos que se busca lograr con el uso de estos sistemas es controlar los niveles de inventario disponible en los distintos puntos de la cadena de suministro (pueden ser almacenes, pero también tiendas físicas, por ejemplo)
Asimismo, es imprescindible establecer alertas que indiquen el momento en el que hay que efectuar el reabastecimiento de determinadas referencias. Estos programas también minimizan los errores humanos en la gestión de procesos.
- Controlar los KPI en la gestión de stock y actuar a partir de los datos
Llevar un control de los indicadores clave en gestión de inventarios es fundamental para evitar incurrir en ineficiencias que puedan originar roturas de stock. Al respecto, destacamos las siguientes estrategias:
- Controlar el punto de pedido: hace referencia al momento en que hay que emitir un pedido de reposición al proveedor. El punto de pedido debe estar en continua revisión, ya que determina el nivel de existencias mínimo que puede mantener la empresa para así evitar roturas de stock.
- Marcar las cantidades que se tienen que adquirir en función de indicadores como la rotación de mercancías, el índice de cobertura (muestra para cuánto tiempo dispone la empresa de existencias), y la ocupación del espacio de almacenaje.
- Contar con suficiente stock de seguridad para paliar las desviaciones que puedan producir la demanda o los proveedores, pero sin incurrir en un sobredimensionamiento de las existencias en el almacén.
- Adoptar un sistema de inventario permanente
En ocasiones, la rotura de stock se produce por no ser capaz de localizar los productos dentro de la instalación, aun estando disponibles en el inventario de la empresa.
Esta es una de las complicaciones que se resuelven implantando un SGA que permita operar con un sistema de inventario permanente: la solución ideal para aquellas empresas que cuentan con un número de referencias complejo y elevado.
En este sentido, el software de gestión de almacén garantiza el acceso a los datos de stock en tiempo real, pudiendo controlar qué hay en el almacén y dónde se encuentra.
Además, informatizar la base de datos de las existencias permite analizar el histórico y ver las fluctuaciones del stock para así identificar productos clave para la empresa.
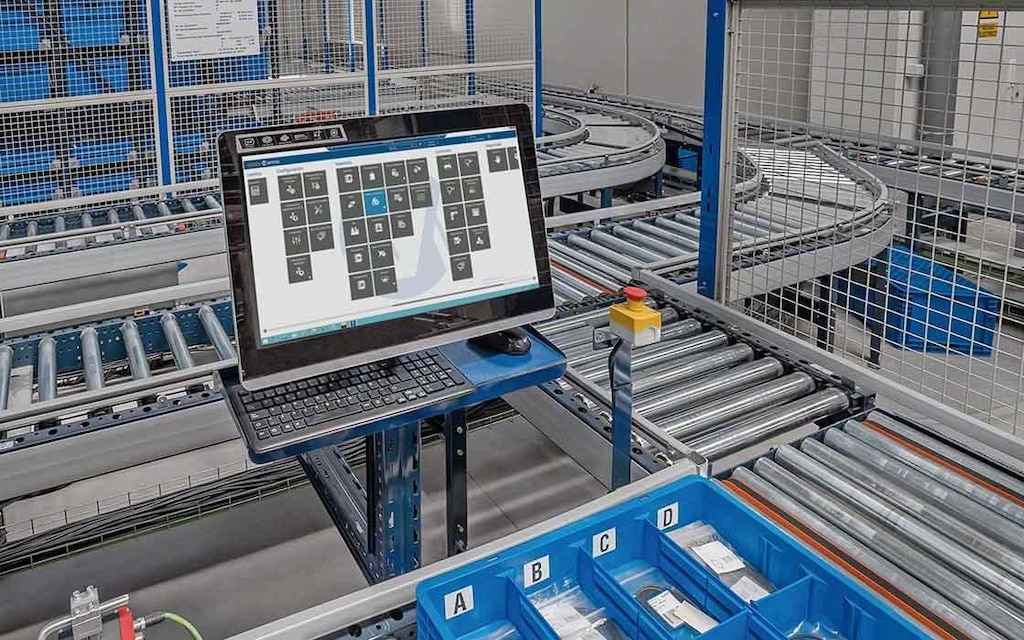
- Automatizar los procesos intralogísticos y reducir el deterioro de mercancías
En todo inventario se dan mermas, es decir, pérdidas de mercancía por deterioro, mala conservación, errores en la manipulación e incluso por hurtos o robos.
Esta es una cuestión que hay que tener controlada para que las mermas no precipiten roturas de stock. Sin embargo, es posible poner en marcha medidas que las reduzcan al máximo, como por ejemplo:
- Establecer accesos limitados a la base de datos del inventario. Esto es sencillo con un SGA como Easy WMS de Mecalux, ya que es posible gestionar los accesos al sistema por parte del equipo de trabajo y prevenir manipulaciones indeseadas.
- Automatizar el manejo de cargas, ya que mejora mucho la seguridad de todos los movimientos y evita accidentes que puedan dañar la mercancía y al personal. Además, el uso de máquinas también refuerza el respeto a los flujos de mercancías FIFO o LIFO.
- Controlar de forma automática la identificación de referencias y el volcado de datos en el sistema. Por ejemplo, esto se consigue con elementos como los PIE (Puestos de Identificación de Entradas), que garantizan la fiabilidad de los datos que muestra el SGA.
En definitiva, a pesar de la máxima que reza “el stock más rentable es el que no tengo”, el inventario es un elemento regulador necesario para el correcto funcionamiento de la cadena de suministro.
Evitar las roturas de stock se convierte entonces en un claro objetivo de toda empresa que quiera proteger su rentabilidad. Las nuevas tecnologías como el software de gestión de almacén o los sistemas automáticos están facilitando su consecución.