El pavimento de un almacén es un elemento clave del mismo porque es la base de todo. Todas las actividades que tengan lugar en el almacén van a ocurrir encima de este pavimento y es por ello que es muy importante prestar una especial atención a todo lo relacionado con él, desde los tipos de cargas que soportará hasta el sustrato o la capa de acabado.
Tipos de cargas
Hay que tener en cuenta que no todas las cargas que debe soportar esta base son iguales. De hecho, es esencial que el pavimento sea capaz de soportar cargas muy elevadas de dos tipos: estáticas y dinámicas.
Cargas estáticas
Estas cargas se generan bajo los pilares de las estanterías. Son de tipo puntual, de gran intensidad, concentradas en una muy pequeña superficie y están distribuidas equitativamente sobre todo el emparrillado del suelo del almacén. Resultan muy desconcertantes para la mayoría de los constructores y les causan un elevado grado de alarma, ya que alcanzan valores de 7 u 8 toneladas e incluso bastante más, concentradas sobre una reducida superficie –la de la sección del perfil del pilar– de entre tan sólo 80 o 100 cm2.
![]() |
![]() |
|
Estudio de la carga nominal que deben soportar las estanterías. | Análisis del pavimento en el proceso de construcción de un almacén. |
Cargas dinámicas
Las cargas dinámicas las producen los aparatos de manutención circulando sobre pasillos muy estrechos y son también muy fuertes y varían en función del tipo de máquina que se utilice. En el caso más extremo, como es el de un transelevador, el peso puede alcanzar las 18 t y estar concentrado sobre una superficie mínima, la que representa la huella de la rueda de carga. Sin embargo, este efecto queda fácilmente minimizado ya que se reparte sobre todo el carril guía por el que se desplaza la máquina.
En otros tipos de elementos de manutención, las cargas más pesadas se producen cuando están parados. Un ejemplo muy significativo es el de las carretillas trilaterales, cuyo mayor efecto sobre el suelo se produce cuando están depositando o tomando un peso a máxima altura y tienen las horquillas extendidas lateralmente. En ese momento, la presión que se ejerce sobre las ruedas de carga alcanza valores tan altos que pueden llegar a sobrepasar los límites de resistencia del suelo, así como de las propias ruedas y sus rodamientos. Este esfuerzo se transmite directamente a los laterales de los pasillos.
Otras máquinas, como las carretillas elevadoras contrapesadas, producen la máxima presión sobre el suelo cuando están descargadas y lo hacen con las ruedas traseras, ya que en esa parte es donde descansa el contrapeso; cuando la carretilla está cargada, se produce una nivelación de carga en la parte delantera (por el principio de palanca) y, aunque el peso total aumenta, está repartido a lo largo de toda la superficie de la máquina. En este caso, la carga también es soportada en una pequeña superficie, la de la huella de los neumáticos.
¿Qué se entiende por un pavimento adecuado?
La misión de un pavimento (y su cimentación) es la de soportar y transferir las cargas desde la superficie del suelo hacia abajo hasta que alcancen el nivel del subsuelo. Esto es aplicable tanto para las cargas dinámicas como para las estáticas. Por lo tanto, el suelo adecuado es el que posee la dureza y la estabilidad necesarias para cumplir con estos cometidos.
Es fundamental observar las especificaciones de nivelación del suelo para garantizar el correcto funcionamiento del almacén.
El acabado de la superficie debe estar correctamente nivelado dentro de los márgenes y tolerancias que implica la utilización de un determinado tipo de instalación, con una maquinaria específica y un sistema particular de almacenaje. El conseguir estos objetivos y cualidades es responsabilidad de diseñadores y constructores.
La importancia del sustrato
Antes de iniciar la instalación de un buen suelo para un almacén, es indispensable examinar el sustrato o capa firme sobre la que se ha de apoyar firmemente el pavimento. El sustrato es muy variable y puede presentar enormes diferencias entre dos lugares, aunque estén muy próximos e incluso dentro de un mismo espacio por lo que las variaciones entre unos y otros puntos del mismo local pueden ser sustanciales.
Los parámetros más destacados que se deben observar en el sustrato son su resistencia a la compresión, su tendencia al deslizamiento y su posibilidad de absorción de agua. Para conocer los valores de estos factores en un lugar determinado y descubrir cómo varían a diferentes profundidades, es necesario realizar unos análisis in situ.
Es imprescindible asegurarse de que el sustrato del almacén proporcionará un comportamiento totalmente adecuado a la carga que se va a colocar sobre el pavimento que descansará sobre él. En función de los resultados obtenidos con los exámenes necesarios, se elige el lugar y la zona precisa en donde se debe levantar la instalación.
Las características de esta parte tan importante del suelo influyen decisivamente en la cimentación. Para la realización de esta se pueden usar desde simples almohadillas de soporte o bandas de mayor o menor anchura hasta, en los casos más extremos, un emparrillado completo. En algunas ocasiones, las características del sustrato fuerzan a variar la posición de los pilares de las estanterías, a fin de que estos coincidan con los puntos que ofrecen las necesarias garantías.
Composición del pavimento
Sobre el sustrato se levanta el pavimento en sí. Este suele estar formado por una subbase de material aglomerado firmemente compactado para soportar la carga. Esta capa está compuesta por cualquier tipo de material, ya sea natural o de relleno. Sobre la subbase, se acomoda una losa de hormigón destinada a soportar la presión.
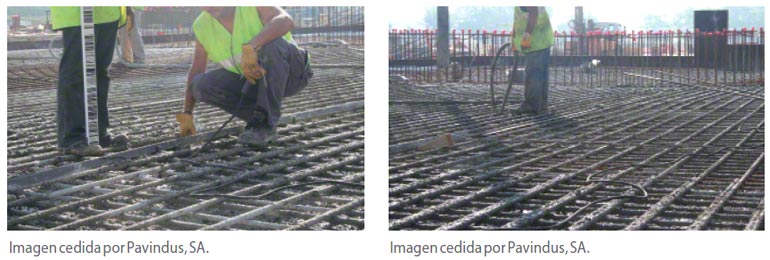
Se puede incluir también un refuerzo a base de barras de acero, con el que se consigue aumentar la resistencia de la capa curada, pese a las inevitables contracciones y deslizamientos que sufre el hormigón durante el proceso. Se incluya o no ese refuerzo, es inevitable que puedan aparecer grietas en las losas curadas, incluso aunque se tenga el cuidado más extremo en su construcción. Si estas grietas se producen de una forma casual y no controlada, la imposibilidad de efectuar un relleno adecuado, dada la irregularidad de las mismas, provoca siempre problemas de fluctuación de las cargas.
Es frecuente inducir el agrietamiento para que estas aberturas aparezcan en lugares concretos que se puedan observar y controlar. Esto se hace mediante el serrado de la losa a lo largo de una determinada tira, con un corte de una profundidad de entre un cuarto y un tercio del grosor de la capa. De esta forma, la rotura se desarrolla en esa posición y no en otra, y puede ser fácilmente rellenada de una forma sencilla y limpia.
Juntas en el pavimento
Las juntas que se pueden encontrar en los suelos de las instalaciones pueden tener diversos orígenes: estar producidas por tiras individuales a lo largo del pavimento, ser el resultado de la misma construcción –producidas por el final de un día de trabajo y el comienzo del siguiente–, haber sido creadas para evitar o rodear columnas o muros, o haber sido producidas mediante cortes de sierra. Sea cual sea su origen, pueden ser una fuente de problemas, porque se pueden descarnar por el paso continuo de las carretillas.
Las juntas han de estar enlazadas o empernadas con la estructura de la subbase para evitar que se transfieran movimientos por debajo de las losas adyacentes. En las juntas de dilatación, los pernos deben estar convenientemente empotrados y situados de manera totalmente alineada. Estos pernos tienen que tener un extremo de deslizamiento libre dotado de un manguito de plástico embebido en una de las losas.
Por otra parte, las juntas de dilatación han de tener una anchura proporcional al espesor de la losa, aunque nunca de más de 10 mm. Si bien se pueden practicar en cualquier punto, siempre es preferible hacerlo evitando los lugares donde se producen muy altas cargas puntuales, es decir, lejos de los puntales de las estanterías.
Almacén para una empresa dedicada a la electrónica de consumo
La capa de acabado
Sobre la subbase y la losa se instala una tercera capa, la de acabado. Es monolítica y es la que forma la superficie de trabajo propiamente dicha. Habitualmente, la capa de acabado está compuesta por una mezcla de cemento granulítico de unos 50 mm de espesor. La suavidad, dureza y las cualidades para el trabajo de dicho material son las más adecuadas para que el pavimento soporte las condiciones que se producen en el uso de máquinas en el almacén.
El hormigón granulítico se aplica sobre la losa húmeda de hormigón industrial, formando un bloque con ella y heredando, por lo tanto, sus juntas. En este punto se plantea una cuestión que hay que decidir: ¿debe realizarse la capa de acabado junto con la losa y, de este modo, estar también sujeta a sus problemas y tratamientos, sobre todo en lo referente a las juntas? ¿O debe instalarse de manera totalmente independiente?
Se puede aplicar esta capa de forma independiente y separada sobre una losa seca, pero entonces se requiere que el espesor de esta última sea, como mínimo, de unos 125 mm. En este caso, se habilita una nueva capa de hormigón con los mismos problemas de fragilidad y abarquillamiento de la losa principal, ya que la superficie de acabado se comportará y se contraerá de manera independiente.
Para evitarlo, se precisa la incorporación de una nueva película o membrana de separación, que forma una finísima capa en la que no existen juntas apreciables. Mediante la adición de bituminosos o de una amplia variedad de copolímeros se pueden obtener mezclas de hormigón de una extraordinaria fineza. Si se utilizan resinas sintéticas, se puede llegar a lograr una capa de tan sólo 3 mm de espesor, lo que supone un pavimento de un excelente acabado. Por otra parte, si se quiere lograr una superficie más confortable, se pueden utilizar resinas con una mayor resiliencia, es decir con una mayor capacidad elástica para absorber la deformación y para recuperarse cuando se deja de ejercer presión.
Se ha de tener en cuenta, no obstante, que algunas capas obtenidas mediante mezclas especiales pueden carecer de estabilidad o de cualidades granulíticas completas, como es el caso de la utilización de resinas inadecuadas para corregir defectos de la capa superior. Estas mezclas pueden resultar no solamente inestables, sino tremendamente caras.
Los pavimentos para almacenes necesitan, por lo tanto, una elaboración muy cuidadosa y un mantenimiento preventivo durante su utilización. De esta manera se podrán evitar y corregir los desperfectos y descarnamientos que las ruedas de las carretillas producen cuando circulan y atraviesan las juntas. Estas capas de acabado tan exigentes no son necesarias en los almacenes automáticos, ya que no se circula por ellos.
Extendido del pavimento
Una vez explicados los conceptos básicos y los elementos que conforman un pavimento, es momento de pasar a examinar cómo se debe llevar a cabo su construcción. Tras preparar la cimentación y realizar la nivelación de la subbase, se ha de decidir el tipo de bastidor que se empleará y el método de extensión del suelo, que diferirán en función de que se tenga la intención de realizar un pavimento de bajo o alto índice de tolerancia.
El método de extensión del suelo se basa en la utilización de una viga de compactación, manejada por dos operarios, que se dedican a hacer que el hormigón quede perfectamente embebido en el bastidor. Mientras, otros operarios, equipados con una máquina aplanadora, recorren la superficie. Este es un método típico de construcción, pero aunque la máquina aplanadora puede facilitar el suavizado de la superficie no consigue el aplanamiento que se requiere.
El hormigón no debe ser manipulado en demasía, con el fin de evitar que los granulados pesados y los aditivos caigan hacia la parte inferior del pavimento o de la capa. Para conseguir estrechas tolerancias en la superficie de acabado, sin necesidad de un trabajo extraordinario, es preciso que el hormigón no encuentre grandes desniveles u hoyos en la subbase.
Es necesario poner un cuidado extraordinario en que la extensión del pavimento se haga con un alto grado de nivelación, pues en caso contrario, el obtener luego las tolerancias exigidas se hace progresivamente más difícil en cada etapa de la construcción. En este aspecto influye también el bastidor que se utilice. Para un suelo de tolerancia relativamente baja, se puede usar uno de madera, pero cuando se requiere disponer de unas altas tolerancias es preciso emplear, al menos, laterales metálicos.
La razón de esto es que la precisión en la rectilinealidad y nivelación depende del bastidor que se use. Cuanto mayor sea el grado de fiabilidad de este, mejores serán los resultados.
El éxito en la obtención de un pavimento no estriba sólo en la utilización de un bastidor adecuado, sino también en otro factor básico: el equipo humano que lo maneje y su habilidad para manejar los medios mecánicos de compactación y acabado.
Un sistema habitual para la ejecución de un pavimento convencional consiste en la extensión de bandas de hormigón que se van acabando a medida que este se va echando. Este sistema puede presentar dos problemas cuando se trata de pavimentos de alta tolerancia:
- El acceso desordenado a las zonas de relleno durante el proceso de comprobación
- La dificultad física de realizar bandas anchas, por lo que puede ser necesario utilizar tiras estrechas y alargadas
Actualmente se consiguen tiras de entre 9 y 15 m en locales con pavimentos de muy alto índice de tolerancia. Para ello se debe contar con personal muy especializado y utilizar vigas de compactación especialmente diseñadas para este trabajo. En cualquier caso, ya sean anchas o estrechas, el método más empleado consiste en realizar tiras alternas que se van echando y acabando. El resto se completa posteriormente tras un corto periodo de curación.
Resistencia, porosidad, unión y duración de los pavimentos
Además de todas estas características constructivas, los pavimentos de los almacenes deben contar con otras facultades que los hagan especialmente adecuados para el uso al que están destinados.
- Deben ser resistentes a la abrasión, cuestión contemplada en la normativa UNE 41008, la cual establece una escala conocida con el nombre de MOHS, que va del 0 al 10.
- También deben aguantar la compresión, y soportar por encima de los 500 kg/cm2, en las zonas generales. En función de las máquinas que se utilicen, pueden estar obligados a aguantar hasta los 800 kg/cm2 en los caminos de rodadura. En cuanto a las exigencias de la resistencia a la flexotracción, suelen estar alrededor de los 150 a 250 kg/cm2.
- El suelo debe ser resistente a la acción de elementos como el aceite, las grasas y los hidrocarburos ya que, aunque no se almacenen dichos materiales en la instalación, son igualmente empleados en las carretillas e inevitablemente pueden producir manchas en el suelo. En relación a la porosidad admisible, es preciso que esta sea muy pequeña, con valores inferiores al 3%.
- El pavimento ha de formar un monolito conjuntamente con la base de soporte a fin de evitar deslizamientos y movimientos hacia abajo que provoquen baches en la superficie.
- Por último, el suelo ha de ser duradero y resistente al desgaste, aunque es inevitable que con el tiempo se formen las llamadas rodadas, producidas por el paso constante de las ruedas de las máquinas por los mismos caminos una y otra vez, dado su tremendo peso. Estas rodadas pueden alcanzar una gran profundidad y provocar desajustes en la instalación, con el consiguiente riesgo implícito.
La elección de una empresa especializada en la realización de pavimentos para su uso con carretillas de pasillo estrecho es, sin duda, la mejor garantía para una instalación óptima y duradera. El escatimar en este punto puede comprometer seriamente toda la instalación y un proyecto de un altísimo coste puede verse afectado por ahorrar en uno de los aspectos aparentemente menos importantes pero determinantes en la práctica.
Para más información recuerde que tiene a su disposión el servicio de consultoría logística de Mecalux.