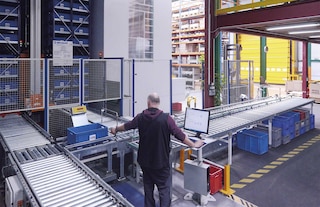
¿Cómo aplicar el ciclo de Deming (PDCA) en logística?
El ciclo de Deming, o ciclo PDCA por sus siglas en inglés (Plan, Do, Check y Act), es un método de gestión de calidad que permite ejecutar una estrategia de mejora continua en la empresa, facilitando así la resolución de problemas de forma estructurada y sistemática.
Este procedimiento está compuesto por cuatro etapas fundamentales: planificar, hacer, verificar y ajustar; de ahí que en español también sea conocido como ciclo PHVA.
El nombre del ciclo toma el apellido del consultor estadounidense que lo popularizó, William Edwards Deming, aunque la creación se le atribuye a su mentor, Walter Shewhart. Deming, experto en sistemas de gestión de calidad y profundo conocedor de estadística, trabajó con ingenieros y científicos para aplicar el círculo PDCA en empresas japonesas a lo largo de los años cincuenta. No sería hasta tres décadas más tarde cuando su metodología en favor de la calidad total arraigaría en la industria de EE. UU.
¿Qué es el ciclo PDCA?
El ciclo PDCA, también denominado espiral de mejora continua, es una metodología orientada a mejorar un procedimiento, localizando la causa de un problema y corrigiéndola. El círculo de Deming normalmente se muestra como una rueda, ya que se concibe como un proceso cíclico. Lo representamos a continuación:
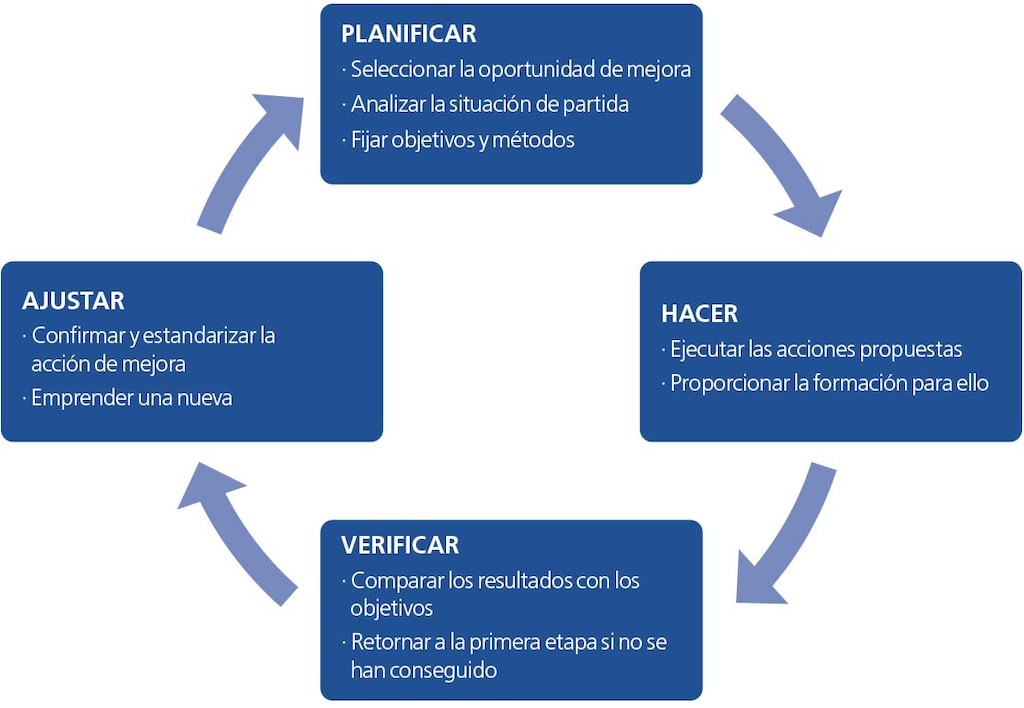
El ciclo PDCA aborda la planificación de una acción de mejora que parte de un problema recurrente, la ejecución controlada de la solución planteada, el análisis posterior del funcionamiento ─para identificar diferencias entre lo planificado y lo ejecutado─ y, finalmente, la estandarización del ajuste correctivo, con el fin de asentar el nuevo proceso optimizado en la empresa.
Las 4 etapas de la rueda de Deming aplicadas a la logística
Abordamos en detalle qué incluye cada una de las etapas del ciclo PDCA:
1. Planificar
El objetivo de esta etapa es definir el problema o el procedimiento que se quiere mejorar. En logística, algunas de las situaciones que merecen ser sometidas al ciclo de Deming pueden ser: errores en las fases de picking y packing, retrasos en la preparación de pedidos, una alta tasa de devoluciones o la entrega de paquetes dañados, entre otras. Llevar un control exhaustivo del almacén a través de unas métricas definidas es esencial para identificar las áreas que están fallando.
Esta etapa del ciclo PDCA se puede dividir en tres subprocesos:
1. Determinar la oportunidad de mejora y analizar la situación de partida: hay que poner énfasis en las causas que están generando el problema, profundizar en los porqués. El Principio de Pareto puede sernos útil aquí. Del mismo modo que es relevante en el método ABC del almacén, esta regla también nos puede servir para fijar prioridades derivadas de un problema logístico. Comúnmente, el grueso de los efectos negativos de un problema (un 80%) son originados por unas pocas causas (un 20%).
2. Establecer objetivos medibles: deben ser específicos, alcanzables, relevantes y orientados a resultados. Además, es necesario designar un marco de tiempo para su evaluación. Estos objetivos pueden estar basados en datos históricos que la empresa haya registrado estableciendo KPI o indicadores clave; o en datos sectoriales fruto de un proceso de benchmarking de la competencia.
3. Preparar el plan de acción: esto incluye estudiar y elegir las opciones correctivas más adecuadas, los responsables de cada acción y las fechas de ejecución. Puede plantearse como una prueba piloto que luego se extienda al resto de áreas si los resultados son satisfactorios.
2. Realizar
La etapa de “hacer” en el ciclo PDCA también es conocida como la etapa de testeo. Consiste en ejecutar la acción elegida y eliminar las causas del problema. Para que se desarrolle sin imprevistos, es conveniente preparar instrucciones y formación para los empleados implicados y registrar toda desviación del plan inicial.
3. Verificar
Se trata de evaluar los resultados , comparando el plan ejecutado con el planteado. A partir de la información recabada, se suelen utilizar herramientas de visualización de datos, con gráficas y diagramas. Un punto importante aquí es respetar los plazos establecidos para no anticiparse y sacar conclusiones precipitadas.
Tras esta evaluación de resultados, pueden darse dos opciones:
- Se ha cumplido el objetivo, de forma que se avanza en el ciclo de Deming hasta la siguiente etapa de ajuste. Es imprescindible comprobar el resto de métricas para que no haya “efectos secundarios”, es decir, que no se hayan descubierto o incrementado problemas en otras áreas.
- No se ha alcanzado el objetivo: si el motivo es que el plan no se ha puesto en práctica del modo adecuado, será necesario volver a la etapa anterior y repasar detalladamente su desarrollo. Si esto se descarta, habrá que retornar al inicio de la rueda de Deming y analizar de nuevo las causas que han dado lugar al problema.
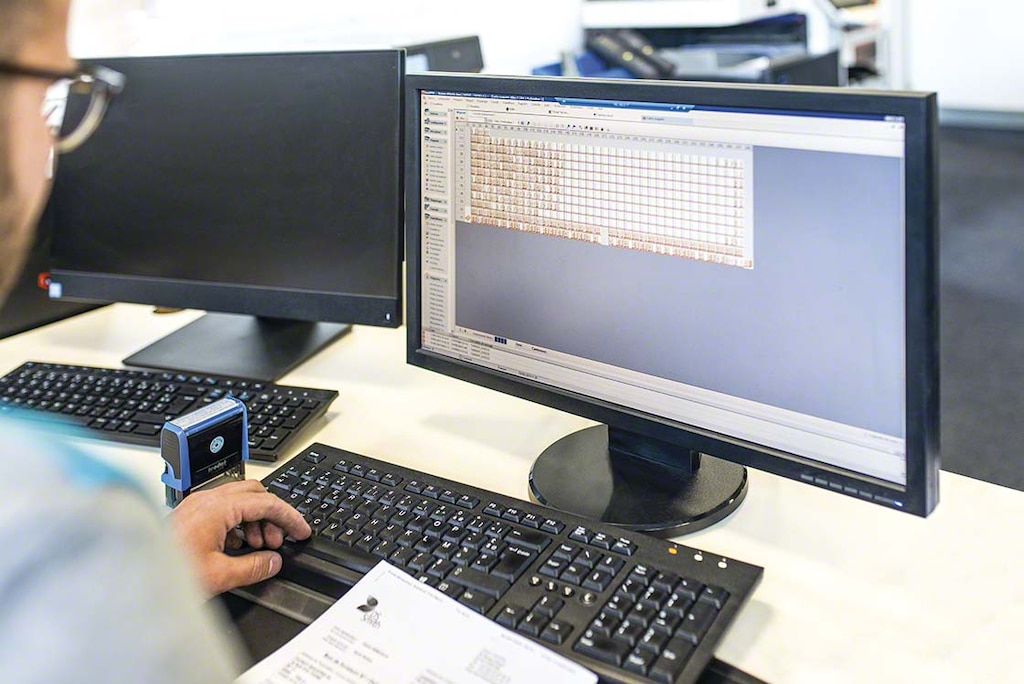
4. Ajustar o actuar
Una vez que el ciclo se ha demostrado efectivo, hay que documentar el cambio, estandarizarlo y controlarlo. Esta información es recomendable ponerla a disposición de la plantilla, organizando, por ejemplo, sesiones de formación. Para un seguimiento exhaustivo de los nuevos procesos, también es pertinente designar los KPI que habrá que vigilar.
Además, si se han probado nuevas herramientas, estas deben aplicarse de manera extendida. Así, si la prueba piloto con dispositivos de picking por voz se ha demostrado eficaz para reducir los errores en la preparación de pedidos, convendrá plantear a los responsables de logística su uso por parte de todos los operarios.
Ventajas del ciclo PDCA
Destacamos los principales beneficios de aplicar el ciclo de Deming:
- Proporciona un método estandarizado que puede ser utilizado en cualquier área empresarial para resolver problemas recurrentes.
- Ahorra tiempo en la búsqueda de la solución más efectiva.
- Funciona como hoja de ruta para asegurar la ejecución completa de un proyecto.
- Garantiza el análisis detallado de errores habituales para su resolución.
- Sirve para controlar y documentar la puesta en marcha de nuevos procesos.
- El ciclo PDCA establece una guía de actuación para eliminar las causas de un problema, independientemente de que haya cambios en el personal.
- Fomenta el trabajo en equipo gracias a la participación activa de todos los implicados.
¿Cómo mejora el PDCA la calidad logística de una compañía?
En logística, calidad supone satisfacer la demanda del cliente al menor coste sin que el nivel de servicio se vea comprometido en ningún momento. La clave está en dar con el equilibrio óptimo entre costes y calidad de servicio.
Los costes de la calidad y de la no calidad
Ligados a este concepto hay dos tipos de costes:
- Costes de calidad: son los derivados de la obtención de la calidad exigida. Por ejemplo, es el coste relacionado con poner en marcha un plan de mantenimiento preventivo industrial en el almacén para la correcta conservación de los sistemas.
- Costes de no calidad: son los que surgen por la falta de calidad en los procesos. Un ejemplo serían las pérdidas como consecuencia de parones o fallos en la maquinaria.
Herramientas para la gestión eficiente del almacén
La mejora de la calidad es un objetivo constante en logística, puesto que es sinónimo de una mayor productividad. La meta final es “hacer las cosas bien a la primera”. Para ello, aplicar métodos como el ciclo PDCA a los procesos en el almacén es clave para incrementar la eficiencia logística de la empresa.
La implantación del ciclo de Deming se puede complementar con nuevos sistemas y equipamiento para optimizar todos los procesos de la instalación. La instalación de un SGA en el almacén potencia la aplicación de este método, ya que este sistema recopila y procesa automáticamente un enorme volumen de información.
Además, herramientas como el Supply Chain Analytics Software facilitan el análisis de estos datos a través de cuadros de mando y gráficos personalizados, lo que incrementa la eficiencia en etapas clave como las entradas y salidas de stock, la preparación de pedidos o la gestión de inventarios entre otras.
La innovación tecnológica potencia el efecto del ciclo PDCA
El objetivo final de la calidad logística es lograr una mejora continua del servicio ajustando los costes al máximo. De hecho, dos de cada diez encuestados en la Supply Chain Digital and Analytics Survey de Deloitte considera la reducción de costes logísticos como el primer objetivo en su apuesta por herramientas de análisis de datos.
La monitorización de procesos asegura el control del correcto desarrollo del ciclo de Deming, que puede aplicarse de manera más efectiva con el uso de sistemas informáticos. Si quieres descubrir en profundidad las ventajas de uso que supone un sistema de gestión del almacén, contacta con nosotros y te enseñaremos su funcionamiento en una demo personalizada.