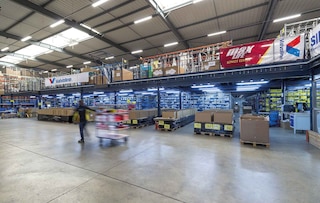
El batch picking o picking por lotes: ¿cuándo aplicarlo?
El batch picking o picking por lotes es un método de preparación de pedidos que se caracteriza por recoger de una vez varias unidades de un mismo SKU para pedidos diferentes.
Tomando un ejemplo sencillo: si vas a hacer la compra para ti, para tu hermano y para un amigo y cada uno necesita seis cartones de leche, cogerías 18 cartones de una vez, para más adelante separarlos y organizarlos en cada cesta de la compra.
Este es un ejemplo sencillo del método batch picking aplicado al recorrido en el supermercado, pero veamos en detalle el alcance de esta técnica en logística de almacenamiento.
Modalidades de picking por lotes o batch picking
La base de la técnica se encuentra en la recogida agrupada de referencias, pero existen distintas variaciones del batch picking:
- Batch picking tradicional: los productos extraídos se depositan directamente en un equipo recogepedidos o en un carro roll container, para llevarlos a una zona de acondicionamiento donde luego se ordenan por pedidos y se consolidan. La ventaja de esta fórmula es que, al no realizar ninguna clasificación en el carro, se pueden coger más productos en un viaje.
- Pick-to-cart o picking con carritos: como el propio nombre indica, se utilizan carritos que los operarios manejan de forma manual a través de los pasillos con estanterías de picking. Estos carritos de picking cuentan con gavetas de plástico identificadas con códigos de barras que hacen referencia a cada pedido. El operario entonces va consolidando los pedidos, es decir, deposita cada referencia en la caja que le corresponde, facilitando después la labor de empaquetado.
- Pick-to-box: se trata de una variación del anterior método, los carritos llevan ya directamente el paquete o la caja de cartón que se enviará. De esta forma, se realizan tres tareas de picking al mismo tiempo: recogida, consolidación y empaquetado. Esta técnica requiere de una coordinación avanzada porque hay que calcular de antemano el tamaño y tipo de embalaje necesario para enviar cada pedido.
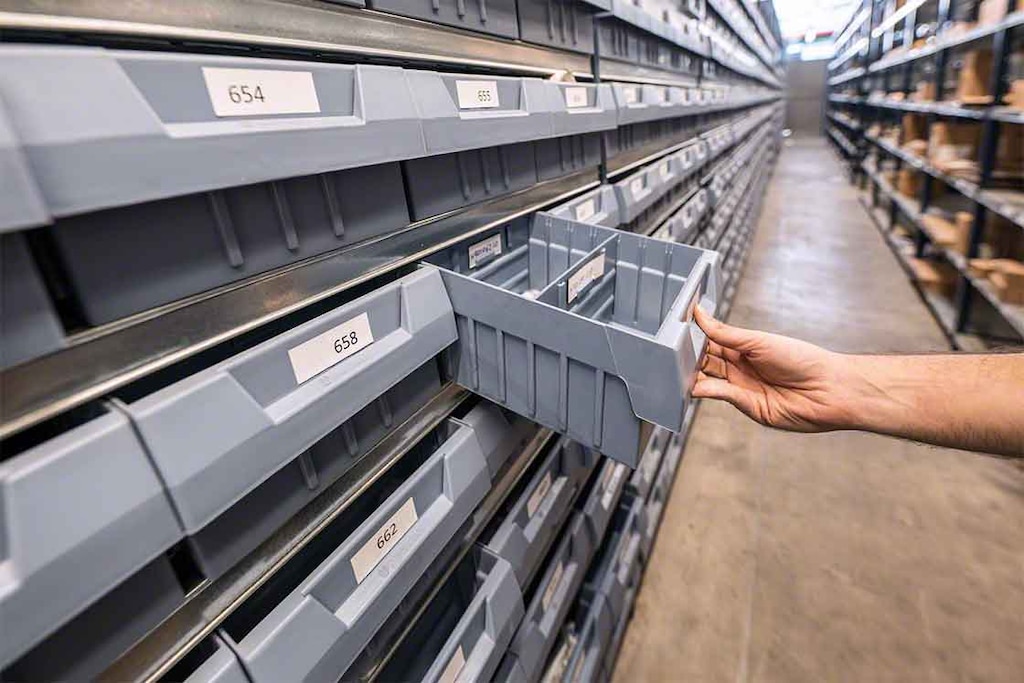
Cuándo aplicar el picking por lotes o batch picking en el almacén
La principal ventaja del batch picking es el ahorro en desplazamientos y en tiempo que supone para los operarios. Si hay diez pedidos que incluyen la misma referencia, con un solo viaje se recoge el lote completo, evitando repetir el recorrido diez veces.
No obstante, para que esto se cumpla, es necesario organizar bien la secuencia de tareas. Por ello, el layout del almacén, la ubicación de cada referencia y la configuración de los lotes deben estar organizados de manera que favorezcan el tránsito de operarios en los pasillos. Así, podrán trabajar al mismo tiempo sin interferencias.
En este sentido, un software de gestión de almacenes es de gran ayuda, ya que permite configurar la operativa de batch picking teniendo en cuenta variables como:
- El tamaño de las referencias: no es lo mismo preparar pedidos de barajas de cartas que de edredones.
- La ubicación de las referencias en el layout del almacén para concentrar al máximo los desplazamientos.
- El número de operarios haciendo picking a la vez, para evitar interferencias entre trabajadores o exceso de tráfico en los pasillos.
- La prioridad de envío de los pedidos. El SGA controla los tiempos de desplazamiento, consolidación y empaquetado para que estén listos en el momento preciso.
Por otro lado, es particularmente recomendable aplicar el batch picking cuando:
- Los productos almacenados son fácilmente manejables de forma manual y cuentan con tamaños similares. Por ejemplo, si se están preparando pedidos de joyas, en un mismo carrito de picking puede llegar a entrar un centenar de referencias con holgura.
- Hay muchos pedidos con una sola referencia. En este caso, el pedido se completaría muy rápido, ya que no haría falta esperar a la recogida de más productos.
Sin embargo, puede darse el caso de que, aun con SGA, el tráfico de operarios sea muy alto o se dispare en picos de actividad logística. Cuando esto ocurre, una forma de insuflar oxígeno a la operativa es aplicar el wave picking o picking por olas, programando períodos limitados dedicados a la preparación de pedidos.
La selección del método de preparación de pedidos es una decisión estratégica. Para ello, no hay mejor compañero que un SGA como Easy WMS: facilita el registro de datos para optimizar toda la operativa e implantar cambios con las fórmulas de picking, incluyendo el batch picking. No dudes en contactar con nosotros: te enseñaremos el potencial de Easy WMS en una demostración personalizada.