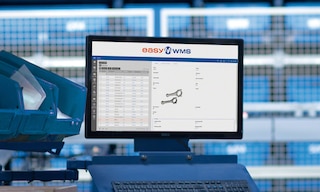
Foncal digitaliza con Easy WMS su almacén de productos de fontanería en Canarias
30 jun 2025Foncal digitaliza su almacén de Tenerife con Easy WMS de Mecalux para mejorar la eficiencia logística y el control de stock en tiempo real. La empresa instalará el software de gestión para mejorar la trazabilidad de sus productos de fontanería y climatización, con vistas a ampliar el sistema al resto de almacenes.