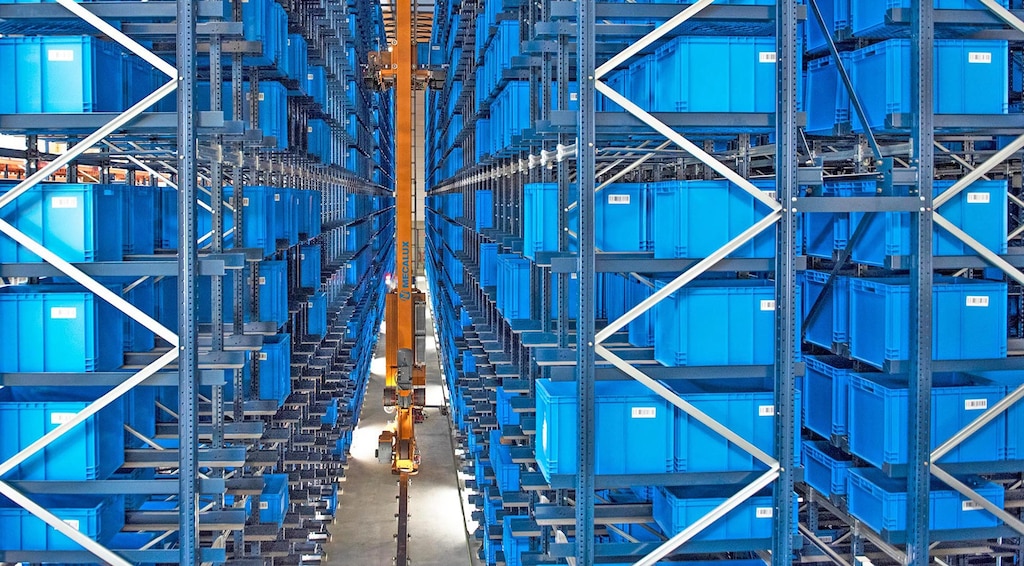
Miniload
El producto
Almacén miniload: almacenaje automatizado para mercancías de pequeñas dimensiones
El sistema miniload es una solución diseñada para el almacenamiento automatizado de cajas y bandejas, ideal para la gestión de referencias de pequeño y mediano tamaño y alta rotación. Integra en un único producto las estanterías, el transelevador, los transportadores y los softwares de control y de gestión del almacén.
El miniload de Mecalux potencia la agilidad y la eficiencia en la preparación de pedidos al automatizar el depósito y la extracción de cargas y favorecer la adopción de estrategias de picking goods-to-person. Además, optimiza el aprovechamiento de la superficie disponible para aumentar la capacidad de almacenaje.
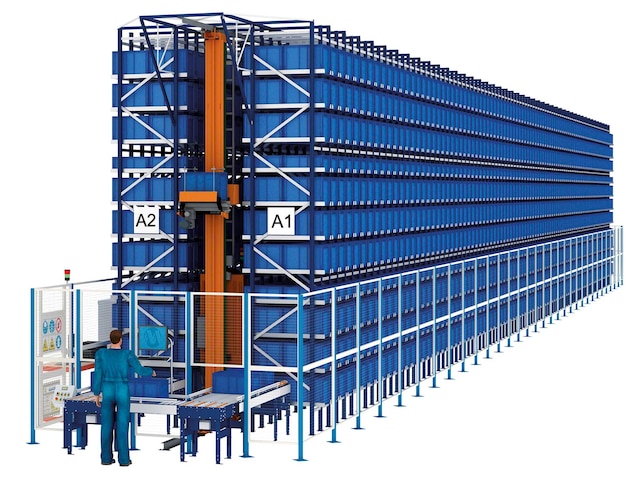
Ventajas del miniload
- Aumento de la productividad: la automatización del almacenaje de cajas y la capacidad de trabajo ininterrumpido 24/7 impulsan el rendimiento y maximizan la eficiencia operativa.
- Picking goods-to-person: las soluciones “producto a persona” simplifican y dinamizan la preparación de pedidos al limitar al mínimo los desplazamientos de los operarios.
- Máximo aprovechamiento del espacio: el transelevador opera en pasillos muy estrechos (de 80 a 140 cm) y puede alcanzar grandes alturas (hasta 20 m), lo que posibilita una gran optimización de la superficie de almacenaje disponible.
- Escalabilidad: su diseño modular facilita la adaptación del sistema al crecimiento de la empresa, por ejemplo a través de la ampliación del número de pasillos y de transelevadores.
- Seguridad: los transelevadores de cajas manipulan la carga con absoluta precisión. Además, su implementación permite reducir de forma significativa el empleo de equipos de manutención manuales dentro del almacén.
- Solución integral: Mecalux diseña, fabrica, instala y pone en funcionamiento todos los componentes del almacén miniload, desde las estanterías y los transelevadores hasta los transportadores, el software de control y el software de gestión.
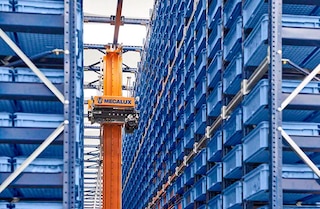
El almacén automático de cajas ha simplificado la gestión de los productos y ha reducido los costes logísticos
Aplicaciones del sistema miniload
Solución idónea para almacenes de cajas y bandejas con alta rotación de producto
El sistema miniload es la respuesta perfecta para las necesidades de almacenaje de las empresas que gestionan mercancías de pequeño y mediano tamaño en cajas o bandejas. El miniload dinamiza las operaciones de preparación de pedidos y optimiza el aprovechamiento de la superficie del almacén.
Cómo funciona un almacén miniload
Automatización total del depósito y la extracción de cajas y bandejas
En los almacenes miniload, el transelevador realiza tres tipos de movimientos: longitudinal (para moverse a lo largo del pasillo, guiado por un carril), vertical (para posicionar la carga a la altura de la ubicación asignada) y horizontal o en profundidad (para que el sistema de extracción se introduzca en la estantería para depositar o extraer la caja).
Testimoniales
Casos prácticos
Ver más casos prácticosModelos de transelevadores para cajas
Transelevadores miniload diseñados para adaptarse a las necesidades de cada empresa
Mecalux ofrece cuatro modelos de transelevadores, lo que favorece una perfecta adecuación del sistema miniload a las exigencias de capacidad de carga, velocidad operativa y rendimiento de cada almacén.
Estaciones de picking
Soluciones para la preparación de pedidos que se ajustan a las necesidades de cada almacén miniload
Mecalux ofrece un amplio abanico de soluciones para configurar puestos de picking que se integren perfectamente en sus almacenes miniload, sea cual sea el espacio disponible, el volumen de trabajo requerido o las características de los productos a manipular. Diseñadas para dar respuesta a los principales desafíos de múltiples operaciones de picking, las estaciones de Mecalux simplifican y agilizan la preparación de pedidos, impulsando la eficiencia y optimizando el rendimiento del almacén.
Componentes del sistema de almacenamiento miniload
El miniload es un sistema de almacenaje integral cuyos componentes principales son el transelevador y su sistema de extracción, los equipos de pasillo, los transportadores y las estanterías.
El transelevador miniload es el equipo encargado de realizar las operaciones de depósito y extracción de las cajas en las estanterías. Está compuesto por distintos elementos que forman una unidad integral.
El sistema de extracción instalado en la cuna del transelevador varía en función del tipo de caja a manipular, del número de unidades a transportar de forma simultánea y del volumen de movimientos requeridos.
El pasillo por el que se desplaza el transelevador está equipado con una serie de elementos que garantizan un movimiento de traslación estable y seguro.
Catálogos
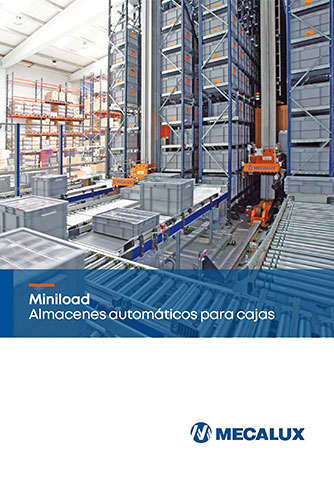


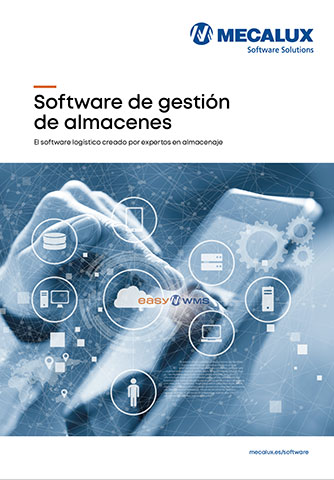
Preguntas frecuentes
El miniload es un sistema de almacenamiento para cajas y bandejas completamente automático. Se trata de una solución integral que incluye las estanterías, los transelevadores para cajas, el circuito de transportadores, el software de control y el software de gestión de almacenes. Su implementación optimiza el aprovechamiento del espacio disponible, dinamiza las operaciones de preparación de pedidos y potencia la productividad del almacén.
El sistema miniload es la solución perfecta para almacenes con alta rotación de producto en los que se gestionan referencias de pequeño y mediano tamaño almacenadas en cajas y bandejas. Por este motivo, su uso es habitual en sectores como el farmacéutico o el alimentario y en almacenes de recambios, piezas y componentes. Asimismo, el miniload es también una opción particularmente recomendable para empresas que gestionan productos de elevado valor económico.
El sistema de almacenamiento miniload es una solución automática que resuelve distintas necesidades y ofrece múltiples ventajas: el aumento de la productividad, la dinamización de las operativas de picking o la optimización del espacio disponible, por ejemplo. Si bien el coste de este sistema es mayor en comparación con el de otras soluciones de almacenaje de tipo manual, los diferentes beneficios asociados a su implementación aseguran un rápido retorno de la inversión.
Sí. El almacén miniload requiere de la implementación de dos softwares: el software de gestión de almacenes (SGA), que gestiona el stock y asigna una ubicación a cada caja, y el sistema de control de almacén (SCA), que envía al transelevador las instrucciones de movimiento. Mecalux puede suministrar ambos softwares.
No necesariamente. En aquellos almacenes en los que la rotación de producto no es muy alta es posible compartir un transelevador entre varios pasillos. Para ello se ha de instalar un puente de transbordo que posibilite el cambio de pasillo del transelevador. Sin embargo, es importante destacar que el sistema miniload alcanza su máximo rendimiento cuando se implementa un transelevador por pasillo.
Las unidades de carga más habituales en un almacén miniload son las cajas de plástico, en especial las 400 x 600 mm y 600 x 800 mm. Asimismo, el sistema también es compatible con el almacenaje de cajas de cartón y de bandejas de plástico o metálicas.
El miniload puede configurarse con estanterías de simple profundidad, que permiten almacenar una única caja por ubicación, o con estanterías de doble profundidad, en las que es posible introducir dos cajas por ubicación.
La capacidad de carga varía según el modelo de transelevador empleado. El ML50, por ejemplo, puede transportar una única caja de hasta 50 kg. El ML100 y el MLHP, en cambio, tienen capacidad para trasladar simultáneamente hasta dos cajas de hasta 50 kg (o una sola de 100 kg). El MLB100Q es capaz de mover a la vez hasta cuatro cajas de 50 kg (o dos de 100 kg).
La altura de los transelevadores miniload suele oscilar entre los 5 y 12 metros, salvo en el modelo MLHP, que puede alcanzar los 21 metros.
La velocidad de traslación del transelevador también varía en función del modelo. El ML50 desarrolla una velocidad máxima de 180 m/min, el ML100 de 200 m/min, el MLB100Q de 250 m/min y el MLHP de 300 m/min.
Los transelevadores para cajas del almacén miniload pueden operar en pasillos de tan solo 80 cm de ancho.
El miniload Mecalux opera en un rango de temperaturas que oscila entre 0 y 40 ºC.
Consulte con un experto