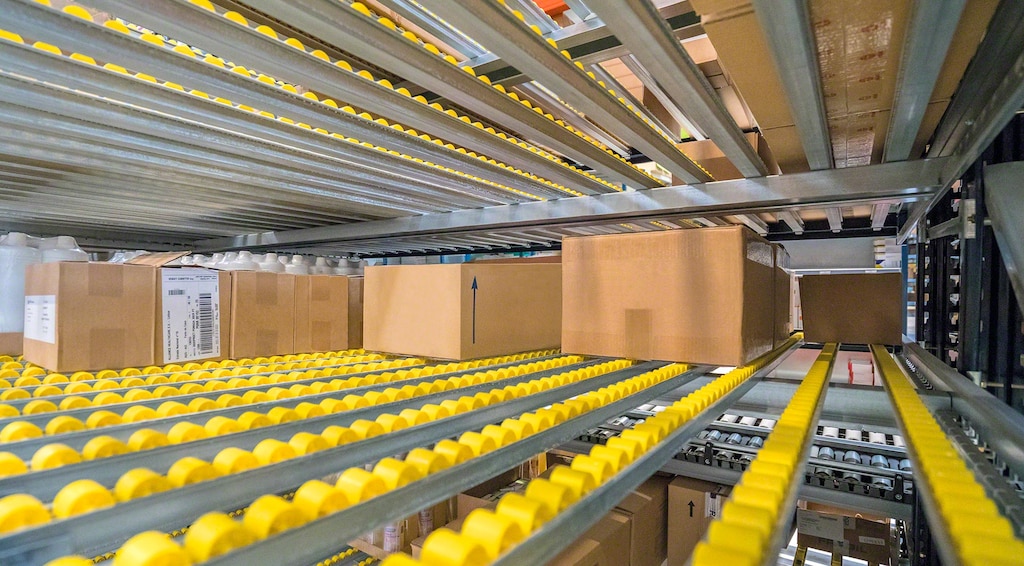
Estanterías para picking dinámico
Sistema de almacenaje por gravedad que agiliza la preparación de pedidos y asegura una perfecta rotación de la mercancía almacenada.
El producto
Picking dinámico: eficiencia y velocidad para la preparación de pedidos
Las estanterías dinámicas para picking, conocidas también como carton flow, son sistemas de almacenamiento por gravedad conformados por plataformas de roldanas ligeramente inclinadas sobre los que se deposita la mercancía, que se desliza de forma autónoma desde el extremo de entrada hasta el de salida.
Esta solución, combinable con la tecnología pick-to-light y con transportadores de cajas, disminuye significativamente el tiempo de preparación de pedidos. Además, al operar según el principio FIFO (first in, first out), garantiza una perfecta rotación de producto y evita cualquier interferencia entre las operativas de reposición y preparación.

Ventajas del picking dinámico
- Mayor velocidad de picking: los niveles inclinados favorecen una excelente visibilidad de la mercancía almacenada y facilitan al operario la recogida de producto. Además, los recorridos para acceder a las distintas referencias son mucho más cortos.
- Mayor capacidad: la supresión de pasillos intermedios que caracteriza a este sistema compacto permite aumentar de forma significativa la capacidad de almacenaje.
- Mayor número de referencias: cada referencia ocupa un único espacio y, detrás de ella, se almacenan las reservas (tantas como permita la profundidad de la estantería).
- Perfecta rotación: se aplica el criterio FIFO (first in, first out: la primera caja en entrar es la primera en salir), lo que garantiza una rotación perfecta de las referencias almacenadas.
- Separación de carga y descarga: las labores de extracción y reposición pueden ejecutarse simultáneamente, ya que se realizan desde pasillos de trabajo diferentes.
- Máxima versatilidad: es posible regular la distribución y el grado de inclinación de los niveles, así como también la disposición de carriles, en función de las dimensiones y el peso de las unidades de carga almacenadas.
- Compatible con pick-to-light: las estanterías para picking dinámico se integran perfectamente con sistemas de pick-to-light, que dinamizan la preparación de pedidos y reducen errores.
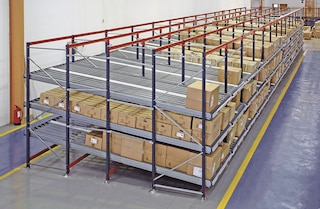
Con las soluciones de picking implantadas hemos aumentado la productividad de nuestro almacén
Aplicaciones de las estanterías para picking dinámico
El almacenamiento dinámico es la solución ideal para almacenes con alta rotación
Las estanterías para picking dinámico son idóneas para almacenes con gran rotación de producto, ya que facilitan y agilizan considerablemente la preparación de pedidos. Su utilización es habitual en empresas de diversos sectores, tanto en almacenes como en centros productivos.
Configuraciones estanterías de picking dinámico
Solución compatible con otros sistemas de transporte y almacenaje
Junto con las diferentes posibilidades de adaptación (distribución e inclinación de los niveles, disposición de los minicarriles, etc.), las estanterías de carton flow pueden adoptar diversas configuraciones en función del modo en el que se integren sistemas complementarios como los transportadores de cajas o las estanterías para palets de reserva.
Casos prácticos
Ver más casos prácticosComponentes de las estanterías de picking dinámico
Las estanterías de picking dinámico son estructuras versátiles que se adaptan con facilidad a múltiples exigencias. Sus características específicas confieren velocidad, eficacia y ergonomía a la preparación de pedidos en todo tipo de almacenes.
Las estanterías tipo carton flow se componen de marcos equipados con minicarrles de roldanas por los que se deslizan las unidades de carga. Un entramado de bastidores y largueros soporta los marcos y confiere robustez y resistencia al conjunto estructural.
Las roldanas son el componente principal de los minicarriles, ya que posibilitan el deslizamiento por gravedad de las cajas desde el extremo de entrada hasta el de salida. En función del tipo de unidad de carga, se instalan roldanas simples, con aletas o alternas.
Las estanterías de picking dinámico incluyen una serie de dispositivos de seguridad (algunos de serie y otros opcionales) que aseguran un movimiento fluido de las cajas a lo largo de los carriles y resguardan la integridad de la mercancía almacenada.
Complementos para estanterías dinámicas para picking
Soluciones auxiliares que dinamizan la preparación de pedidos en las estanterías dinámicas de picking
Catálogos
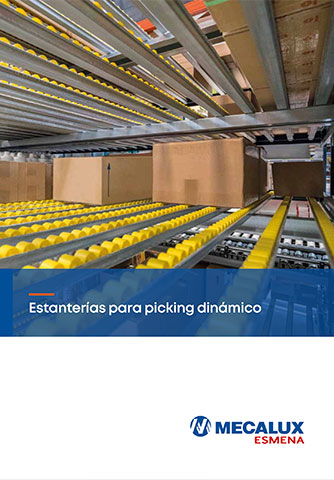
Estanterías para picking dinámico (catálogo)
Reducción del tiempo de preparación de pedidos y perfecta rotación
DescargarPreguntas frecuentes
El picking dinámico, o carton flow en inglés, es una solución de almacenaje conformada por estanterías con niveles ligeramente inclinados en los que se instalan minicarriles con roldanas que facilitan el deslizamiento por gravedad de las unidades de carga, que se acumulan una detrás de otra. Las estanterías para picking dinámico garantizan una perfecta rotación de producto (se sigue el principio FIFO, first in, first out), agilizan la preparación de pedidos (entre otras razones, porque no se producen interferencias entre las operativas de reposición y extracción) y optimizan la superficie de almacenaje disponible, ya que se suprimen los pasillos de trabajo interiores.
Ante todo, no se producen interferencias entre la reposición y la preparación de pedidos, ya que el depósito y la extracción de mercancía se realiza desde pasillos diferentes. Además, estas estanterías aseguran una disponibilidad permanente de producto, ya que facilitan la acumulación de stock de reserva. Complementariamente, los niveles inclinados incrementan la comodidad con la que trabajan los operarios, lo que también dinamiza las tareas de picking. Por último, la integración de soluciones como el pick-to-light o los transportadores de cajas potencia todavía más la eficiencia del picking, ya que permiten disminuir errores y reducir de forma significativa los desplazamientos de los operarios.
La implementación de estanterías dinámicas para picking se recomienda sobre todo en almacenes con un gran volumen de preparación de pedidos y con un número alto de unidades por referencia. Además, es una solución idónea para aquellos almacenes en los que se manejan productos de pequeño tamaño (por ejemplo, empresas del sector de la cosmética y la perfumería) o en los que es necesario adoptar el principio FIFO por la naturaleza de los productos almacenados (como ocurre en el sector farmacéutico a raíz de las fechas de caducidad).
Sí, son totalmente compatibles. De hecho, es habitual que en ciertos sectores productivos se aluda a ellas como estanterías Kanban. Al retirarse una caja ya vacía desde el extremo de descarga de la estantería, se genera un pull, que indica la necesidad de reposición desde el pasillo de entrada. La tarjeta Kanban, que recoge los atributos del producto, se sitúa encima del contenedor vacío para indicar que el carril asignado a esa referencia debe reponerse con stock. La instalación de un nivel superior para el retorno de cajas vacías puede dinamizar esta operativa.
Las estanterías para picking dinámico se adaptan a distintos tipos de cajas y bandejas, principalmente de cartón y de plástico.
Sí, ya que las estanterías de picking dinámico son estructuras muy versátiles que se ajustan con facilidad a distintos tipos de necesidades. Por un lado, es posible modificar la altura de cada nivel de almacenaje (son regulables cada 25 mm) y también su grado de inclinación. Por otra parte, es igualmente configurable la distribución de los minicarriles, cuya distancia de separación puede modificarse para adaptar la estantería a eventuales variaciones en la anchura de las unidades de carga.
No. Las cajas se deslizan sobre las roldanas por efecto de la gravedad, por lo que no es necesario motorizarlas.
La elección de un marco u otro depende tanto de las dimensiones del producto a manipular como de la forma y el tamaño de las cajas utilizadas. Los marcos rectos se utilizan cuando las unidades de carga se extraen completas o cuando se recogen artículos individuales pequeños desde cajas con abertura o semiabertura frontal. Los marcos con bandeja de presentación, en cambio, se emplean cuando se extraen artículos pequeños desde las cajas por la parte superior o productos medianos desde cajas con semiabertura frontal.
Consulte con un experto