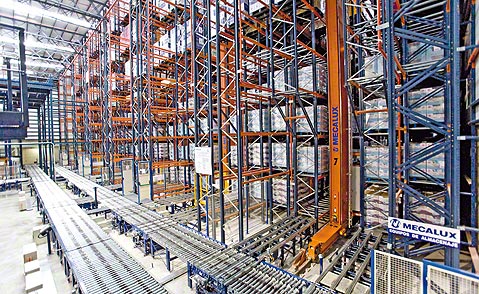
Transelevadores para paletas monocolumna automatizan el silo autoportante de Ubesol
Ocho transelevadores mueven Ubesol
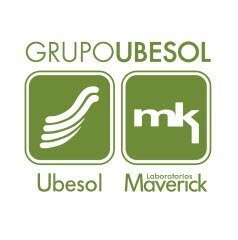
Ubesol fabrica toda una gama de productos destinada al cuidado personal (Ubesol Higiene) y para el hogar (Ubesol Textil) en las tres plantas que posee en España. Una de ellas está ubicada en Ulldecona (Tarragona) y las otras dos en Adzaneta de Albaida (Valencia). Entre ambas se localiza un almacén autoportante unido a la nave de producción mediante una pasarela elevada sobre la calle del polígono. En él siete transelevadores manejan producto terminado mientras el octavo transelevador manipula las cargas de 24 estanterías dinámicas. Este nuevo silo automatizado tiene una capacidad total de 20.000 paletas. Ubesol trabaja con clientes de más de 30 países incluyendo una importante cadena de supermercados con más de 1.000 tiendas en España.
Necesidad del cliente
"La principal razón por la que decidimos instalar un almacén automático ha sido el fuerte aumento de la producción que hemos experimentado para nuestro principal cliente. Desde 1996, momento en el que empezó nuestra relación con esta cadena, los ratios de crecimiento anual han sido del 20%. Eso nos llevó a pensar que necesitábamos una mayor capacidad de almacenaje para los próximos años", dice José García, responsable de la planta de higiene de Ubesol.
Pero la construcción del silo no sólo responde a un aumento en el volumen de paletas, sino también a una cuestión de operativa. "Con la estantería convencional que teníamos antiguamente era costoso manejar grandes cantidades de material. También era difícil dejar todos los pedidos preparados de tal forma que el tiempo de carga fuera el mínimo" explica José García. Los operarios podían efectuar sin ningún problema todas las operaciones que se necesitaban desempeñar para llenar un camión. Los inconvenientes aparecían cuando llegaban más vehículos a las plantas, ya que se empleaba mucho tiempo en la preparación de los pedidos. De hecho, la distancia que había que recorrer para coger las paletas y llevarlas hasta el vehículo era considerable.
Solución propuesta por Mecalux
El nuevo silo instalado con una superficie de 5.000 m2 y capacidad para almacenar 20.000 paletas almacena tanto el producto terminado como la materia prima del tejido que se emplea para elaborar las toallitas. El resto de componentes de fabricación se sigue guardando en cada uno de los almacenes que las factorías conservan.
La entrada de mercancías se produce por la zona de expediciones, que es la antesala del almacén automático, donde se reciben los camiones que transportan materias primas, entre ellas, las bobinas portadoras del tejido. Para poder introducirlas en el interior del silo deben ser paletizadas y pasar por los controles de gálibo correspondientes y el examen por un escáner que lee la etiqueta y envía la información directamente al sistema, para que tanto el SGA como el ERP sean capaces de controlar el stock.
Una vez validados los datos, tanto las bobinas como el resto de materias primas entran al silo autoportante a través de un camino de rodillos.
Allí siete transelevadores monocolumna para paletas, que trabajan a una velocidad de elevación de 36 m/min, ubican las mercancías en 14 estanterías de doble profundidad a la espera de que sean necesarias para fabricar producto terminado, momento en el que se trasladarán a la nave de producción a través de una pasarela en altura que une ambas instalaciones. Sobre esta plataforma se han instalado dos caminos paralelos de rodillos que se desplazan para llevar las mercancías a estas dos plantas. Para poder elevar las materias primas hasta ella se emplea un elevador que las desplaza hasta un transportador de rodillos. Éste las conduce hasta el edificio próximo, en donde un segundo elevador hace descender las paletas hasta el nivel del suelo. A partir de ahí los operarios guían las mercancías hasta el almacén de la nave de producción.
El producto terminado es colocado en paletas completas o en medias paletas y se efectúa la operación de regreso al almacén principal por la misma pasarela pero en sentido contrario por un segundo conjunto de elevadores y un camino de rodillos. A la hora de preparar los pedidos, los transelevadores recogen las mercancías y las depositan en los transportadores para paletas rumbo a la zona de expediciones. En esta área se procede a su almacenaje en estanterías dinámicas que tienen 24 calles con 9.900 mm de profundidad por 8.860 mm de altura y una capacidad para ocho paletas. Aquí otro transelevador maneja las paletas y se ocupa de depositarlas sobre las estanterías dinámicas. Además, esta zona presenta una interesante curiosidad: como la altura desde el suelo hasta el techo es de 9.300 mm se tuvo que llevar a cabo una obra de excavación para instalar el transelevador con el fin de que pudiera desempeñar su trabajo consiguiendo el máximo de capacidad.
Cuando la cadena de supermercados realiza un pedido se vuelca en el sistema de Ubesol y se prepara mediante roll docking, un sistema basado en que la mercancía ha de llegar a los centros logísticos en un momento y en una fecha determinada."Se tiene que garantizar que el pedido llega a su hora. Ello permite planificar mejor la producción y conocer el número de camiones que se enviarán con una anticipación de 15 días", precisa José García. Cuando el camión llega a la instalación de Ubesol, el conductor entrega el número de pedido a los carretilleros, que mediante una pistola de radiofrecuencia lo leen. El dispositivo les indica la ubicación del producto solicitado y los operarios corroboran que se trata de las unidades solicitadas leyendo los códigos de barras con sus terminales de radiofrecuencia. Después, una vez que se han introducido los pedidos en el camión, la cadena de supermercados se responsabiliza de la logística. Ésta confirmará su recepción a Ubesol, que después de volver a comprobar los envíos finalmente los facturará.
Beneficios para el cliente
La automatización del silo ha aportado grandes ventajas para Ubesol, que ha conseguido multiplicar por cuatro el número de paletas que puede ser depositado en sus instalaciones.
- Mejor aprovechamiento de la superficie disponible. "El silo ha concentrado el producto acabado de las dos fábricas, lo cual nos ha permitido liberar espacio que ahora está dedicado a la ampliación de las zonas de producción", explica José García, responsable de la planta en Adzaneta de Albaida. Antes, entre los dos almacenes, el espacio destinado a ello sumaba aproximadamente 5.000 paletas en estanterías convencionales. "Ahora, gracias al que hemos creado, estaremos cubiertos hasta 2015 ó 2018", afirma el responsable de la planta de higiene de Ubesol.
- Economía de tiempos. Para almacenar la mercancía las máquinas se rigen por criterios de proximidad: mediante esta fórmula se logra una mayor agilidad. "Si se almacena al fondo se efectúa un recorrido más largo por lo que las unidades se depositan lo más cerca posible de la cabecera o lo más próximas al túnel de salida cercano a la zona de expediciones", indica José García.
- La automatización de los procesos permite una mejora en la eficacia y elimina los errores de la gestión manual. "Antes los carretilleros llevaban unos listados a partir de los cuales sabían qué productos estaban en cuarentena y cuáles no, pero aun así podían cogerlos. Ahora nunca puede llegar a las estanterías dinámicas una mercancía que está bloqueada", comenta García.
Silo autoportante | |
---|---|
Longitud:: | 99.250 mm |
Anchura:: | 49.650 mm |
Altura:: | 22.230 mm |
Nº de estanterías:: | 14 de doble profundidad |
Nº de pasillos:: | 7 |
Ancho del pasillo:: | 1.650 mm |
Nº de transelevadores:: | 7 |
Nº de niveles de carga:: | 9 |
Altura de los niveles de carga:: | 1.750, 1.800 ó 3.100 mm |
Capacidad por hueco:: | 2 ó 3 paletas |
Unidad de carga:: | paletas de 800/1.200 x 1.200, con alturas de entre 2.200 y 2.600 mm y peso de 500 a 1.000 kg. Unidades de 800 x 1.200 x 1.300 y 600 kg, conformadas por dos medias paletas de 800 x 600 mm. |
Capacidad total:: | 19.824 paletas |
Galería

Almacén automático de paletas servido por transelevadores monocolumna
Consulte con un experto